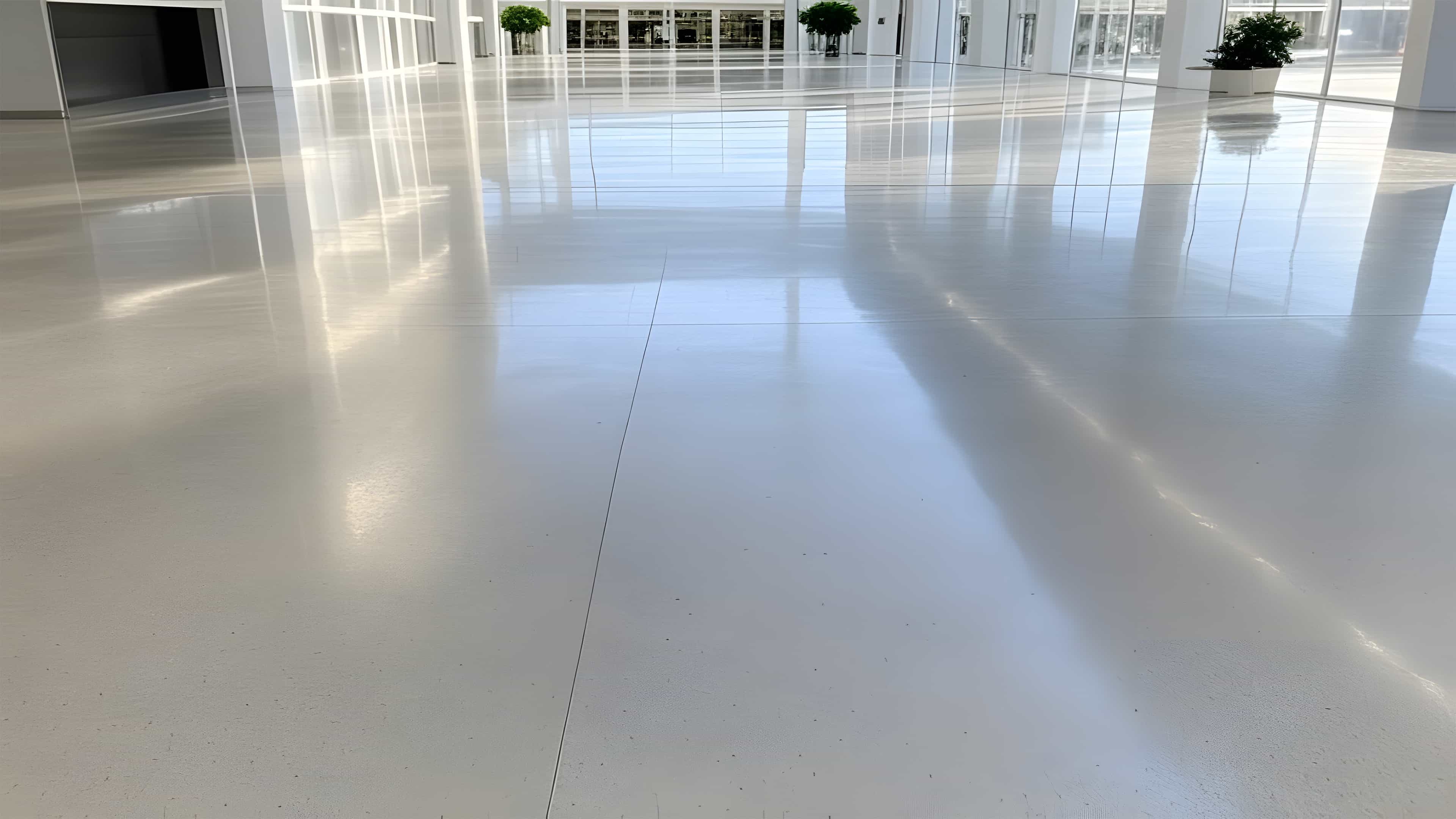
Polished Concrete - The Complete Guide 2025 - Advance Industrial Coatings
More and more commercial spaces and industrial facilities are embracing polished concrete flooring as their preferred surface solution. Major retailers like Costco, Home Depot, Walmart, and Target have made it their standard flooring choice, while restaurants, warehouses, automotive shops, and corporate offices are increasingly converting to this versatile option. The appeal is clear-polished concrete offers an elegant alternative to traditional surfaces like marble, granite, tile, vinyl, VCT, or hardwood floors, all while providing superior durability and lower maintenance requirements.
The growing popularity extends beyond commercial applications. Modern residential spaces are incorporating polished concrete for its contemporary look, exceptional longevity, and remarkable ease of maintenance-creating spaces that are both beautiful and highly functional.
Are you considering Polished Concrete Floor or looking for a trustable contractor to provide Concrete Polishing Services? Here is your must-read POLISHED CONCRETE COMPLETE GUIDE 2025 revision.
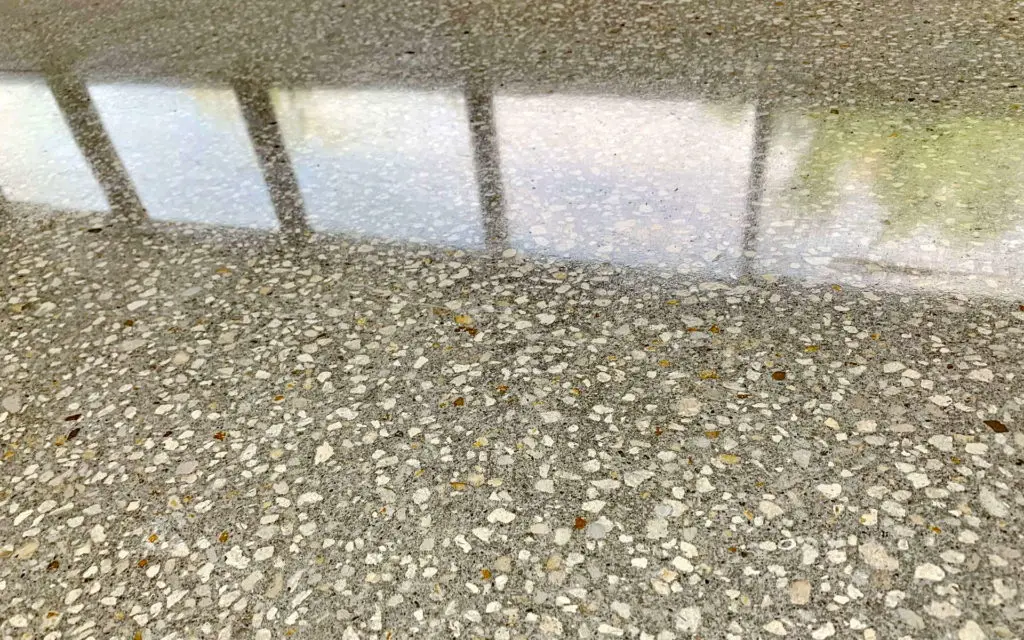
POLISHED CONCRETE: THE COMPLETE GUIDE
CHAPTERS
1. Polished Concrete Fundamentals
What is Polished Concrete Floor?
Polished concrete is concrete that has been processed through a series of mechanically ground "polishing/grinding" steps utilizing professional equipment designed for concrete polishing. This process also includes the use of a concrete densifier/hardener which penetrates into the concrete and creates a chemical reaction to help harden and dustproof the surface. During concrete polishing, the surface is processed through a series of steps (in general, a minimum of 6-8 grinding steps of processing is considered polished concrete) utilizing progressively finer grinding tools. The grinding tools are progressive grits of industrial diamonds in a bonded material such as metal/hybrid/resin often referred to as diamond polishing pads.
Concrete is not considered well polished before 800 grit, and it is normally finished to either the 800, 1500, or 3000 grit level. Dyes designed for concrete polishing are often applied to add color to polished concrete as well as other options such as scoring, creating radial lines, grids, bands, borders, and other designs.
2. Why Polished Concrete
Why Choose Polished Concrete Flooring?
Simply put, a polished concrete floor system transforms a porous concrete floor into a tightened surface, dense enough to keep water, oil, and other contaminants from penetrating the surface.
Here are some of the benefits of concrete floor polishing:
- Elegance and Attractive - Looks amazing & professional. It can be dyed to match any color scheme. Polished Concrete, much like marble, never goes out of style.
- Very Strong and Durable - Extremely tough and resistant, and is able to withstand the pressure and weight from heavy equipment. Surface cannot be easily scratched. High Resistance to foot traffic means it can stand up to the everyday wear and tear of retail or even industrial work spaces.
- Less Maintenance, Easy to Clean - Polished Concrete requires minimal maintenance and is very easy to clean. Less extensive scrubbing or constant refinishing with wax.
- Extended Long Life-Span - Properly maintained polished concrete floor can last years. Refurbish needs a fraction of the cost of other systems, extending the life much farther.
- Highly Cost-Effective - Most polished concrete floor installations are quite cost-effective. The savings are even more significant if you factor in maintenance costs over lifetime .
- Hygiene Friendly - Properly polished concrete can be virtually resistant to fluids, providing waterproof barriers to prevent contaminants from getting to the concrete. It typically contains no noticeable VOC's, making it friendly for any USBG LEED project.
- Minimum Downtime - Polished concrete areas can be put into service immediately after process is complete. It can also be installed while the facility is still in full production.
- Better Ambient Lighting - The High light reflectivity is another important benefit, especially for office, stores, restaurants etc., to project a bright, clean, professional image.
Here is our blog post for you to learn more about the Pros and Cons of Polished Concrete.
3. Concrete Polishing Process
Currently, the industry breaks down the process of polished concrete into grinding and polishing. Some simply use the word "polishing" for the whole process. Each phase is then broken down into multiple steps, consisting of consecutively finer grit abrasives. Every step is refined to its purest possible form on a microscopic level from one progressively finer abrasive to the next until the desired level of 'polishing' is achieved.
The RetroPlate Concrete Polishing System we used and recommended follows these basic steps performed by certified applicators ensuring that every floor turns out just right.
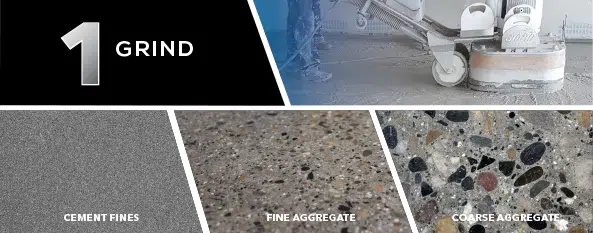
The first step is to grind the floor with industrial strength diamonds. Grinding removes imperfections, marks and scratches, and exposes bare concrete by removing existing coating or mastic. Grinding can be light to heavy depending on the desired level of exposed aggregate.
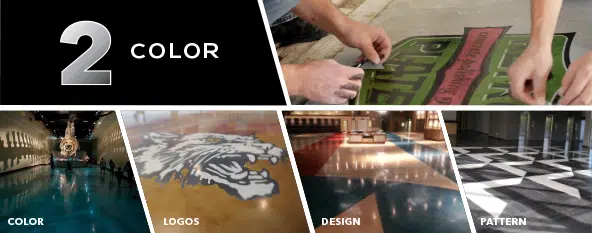
Add style and personality to your polished concrete floors with an array of color options. Achieve any look and style with full color floors, custom logos or unique patterns. Color options for polished concrete include: integral color, dry shake and topical dyes and stains.
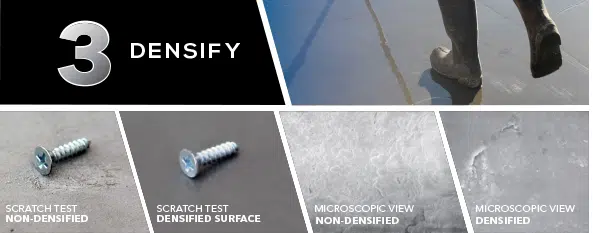
The next step is to densify the floor with RetroPlate. RetroPlate penetrates the concrete and chemically reacts to harden and densify the floor by filling-in pores and creating a dense surface. Densification is key to the long-term benefits of polished concrete. Many densifiers on the market claim to work for polished concrete, but there is only one RetroPlate.

The final step is to polish the floor with progressively finer diamond grits. This polishing procedure is what produces the floor's sheen. A floor can be polished to a flat (ground), satin (honed), polished or highly polished finish. Adding color or seeded material allows for unlimited possibilities in design.
Recent advances in polishing equipment and techniques have allowed concrete to be ground, honed, and polished to a high polish with clarity of reflection and depth. The process is performed with large planetary head machines where the main head rotates in one direction and smaller satellite heads spin in the opposite direction.
The result is a beautiful, durable and efficient surface that eliminates the need for carpets or tile that requires expensive replacement, maintenance, and use of harsh cleaning chemicals.
4. Options & Choices
There are many options available for different Polished Concrete designs. Different Aggregate Exposure, different Clarity of Reflection, and different dyed Color will change the visual aspects and physical characteristics of your polished concrete floor significantly. So know your options and potential outcomes before you make choices.
4.1 Aggregate Exposure
The Aggregate Exposure of the floor represents the amount of aggregate that will be exposed at the surface. Consider the needs and functions of your building when deciding whether aggregate exposure is appropriate. Grinding the concrete to expose aggregate may be considered attractive for a commercial space, but it can be unsuitable for a manufacturing space where dropped fasteners need to be easily spotted on the floor.
Below are the three aggregate exposure levels specified by Concrete Polishing Council CPC for polished concrete floor finishes.
Class A - Cement Fines (Also Called Light Sand / Cream Finish)
Class A is defined as 85 - 95% Cement Fines and 5 - 15% Fine Aggregate. The cement fines finish typically exposes only the sand particles in the concrete floor. This finish is considered a "creamy looking" surface and is the most popular choice for Architectural Ground & Polished floors.
Class B - Fine Aggregate (Also Called Salt & Pepper Finish)
Class B is defined as 85 - 95% Fine Aggregate and 5 - 15% Blend of Cement Fines and Coarse Aggregate.
The Fine Aggregate finish (Salt & Pepper) exposes a spattering of fine aggregate in the concrete floor. This finish is most often chosen to give the appearance of an aged surface. Approximate surface cut depth 1/16 inch.
Class C - Coarse Aggregate
Class C is defined as 80 - 90% Coarse Aggregate and 10 - 20% Blend of Cement Fines and Fine Aggregate. Coarse Aggregate finish typically exposes the greatest amount of aggregate in the concrete floor. The finish is the most often chosen when the substrate has been seeded with custom aggregate. On some floors including restoration of older concrete, there may be limitations to how deeply the floor can be cut. Approximate surface cut depth 1/8 to 1/4 inch.
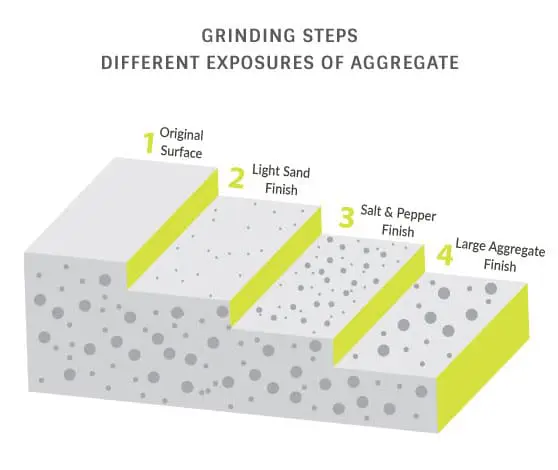
Polished concrete aggregate exposure levels
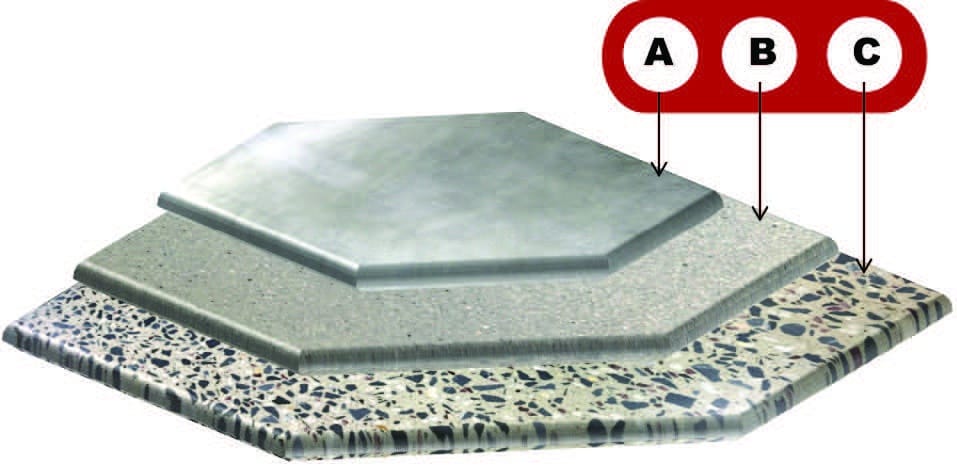
Aggregate exposure chart showing different levels of concrete grinding
4.2 Gloss Level
Depending on the diamond grit used to polish a concrete floor, you can achieve different levels of sheen, from matte to a glassy mirror-like finish. Here are the four levels of polishing and the degree of shine you can expect to achieve at each level.
Level 1 Flat (Ground) - Image Clarity Value 0-9%
A level 1 ground polish usually can be obtained by stopping below the 100-grit resin bond. When you look directly down at the floor, it will appear somewhat hazy with little if any clarity or reflection.
Level 2 Satin (Honed) - Image Clarity Value 10-39%
A level 2 honed polish is obtained by stopping at the 400-grit resin bond, producing a low-sheen finish. When you look directly down at the finished floor and at a distance of roughly 100 feet, you can start to see a slight overhead reflection. This grit level produces a low-luster matte finish.
Level 3 Polished - Image Clarity Value 40-69%
A level 3 polish is achieved by going up to an 800-grit or higher diamond abrasive. The surface will have a much higher sheen than that of level 2 finish, and you'll start to see good light reflectivity. At a distance of 30 to 50 feet, the floor will clearly reflect side and overhead lighting.
Level 4 Highly Polished - Image Clarity Value 70-100%
This level of polish produces a high degree of shine so that when standing directly over the surface, you can see your reflection with total clarity. Also, the floor appears to be wet when viewed from different vantage points. A level 4 polish is obtained by going up to a 3,000-grit resin-bond diamond or by burnishing the floor with a high-speed burnisher outfitted with specialty buffing pads.
4.3 Coloring
How to color or dye concrete? There are 6 ways concrete is colored:
- Integral - Performed at the time of pour and is considered environmentally friendly.
- Integral by seeding a cement/pigment mixture in the top region during power trowel finishing
- Penetrating Water Based Dyes - Performed during the polishing process and is considered environmentally friendly.
- Penetrating Solvent Based Dyes - Performed during the polishing process and is not considered environmentally friendly.
- Penetrating Acid Stain - Performed during the polishing process and is not considered environmentally friendly.
- Colored penetrating surface sealers which are also film-forming and thus produce a more solid color - Considered environmentally friendly
Different manufacturers offer different coloring choices to polished concrete customers. Here is the 24 stock colors covering the most common color choices seen in floors today offered by Ameripolish. Custom colors are available upon request.
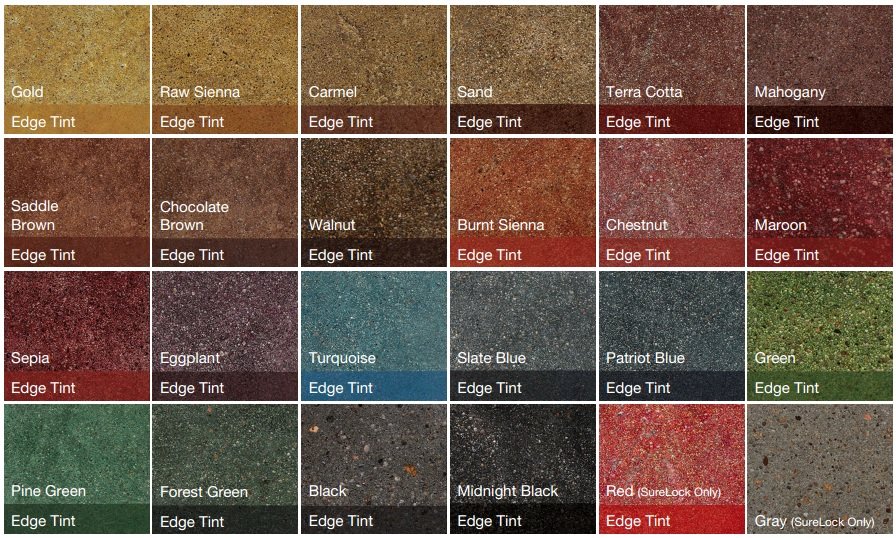
Polished Concrete Dye Colors
5. How Much Does Polished Concrete Cost
Polished Concrete project cost can vary widely based on factors including concrete condition, job size and location, aggregate exposure, gross level and coloring selection etc. For a fairly smooth floor, that requires only a few levels of grinding, $4 sq. ft. is the basic cost for a polished concrete floor. If the floor requires more in-depth grinding or includes coloring with stains and dyes or other special finish designs, then the price ranges between $4-$8 sq. ft.
Smaller residential floors tend to be a bit higher in price because of the requirement for smaller equipment, which will relatively lower work efficiency and special design requirements.
6. Expectations and Limitations
Unfortunately, NOT all concrete is a good candidate for concrete polishing. When working on existing concrete, results largely depend on the concrete quality a contractor is given to work with.
Most existing commercial concrete that is of sufficient strength and hardness will allow for excellent results.
Variables such as aggregate, color variations, miscellaneous contaminates, cracks, patterns left by previous floor covering, existing stains, nail holes, patched areas, and flatness can affect the final appearance and results significantly.
A slab newly poured based on specifications designed for polished concrete finish will eliminate a significant number of variables and provide improved finish results over an existing finished concrete slab.
For projects in the early design phase incorporating a polished concrete floor finish, the Concrete Polishing Council (formerly CPAA) of the American Society of Concrete Contractors (ASCC) advises including their design and construction recommendations in the Division 03 cast-in-place concrete specifications, as prepared by the project's structural engineer.
Download the PDF version of this Polished Concrete Recommended Spec Here.
7. Frequently Asked Questions
Is Polished Concrete Slippery?
Because of polished concrete's unique shine and high reflectivity, many people question if it is slippery. Generally speaking, when the concrete is clean and dry, it is generally no more slippery than plain concrete surfaces. In fact, polished concrete tends to be less slippery than waxed linoleum or polished marble.
There are also anti-slip conditioners that can be applied to a polished concrete floor for extra protection against accidents. The special additives in these products are designed to improve traction and make wet surfaces safer. No additional cleaning is required, but normally it needs to be reapplied periodically.
Certain Concrete Polishing Systems can fall within OSHA and ADA recommendations for coefficient of friction.
Click here to review the RetroPlate Coefficient of Friction Testing Report.
When Can the Floor be Used after the Concrete Polishing Process is Complete?
The floor can be used immediately. There is no drying or waiting time.
How Long Does the Application Process Take?
This depends entirely upon the preparation and layout of the floor. Application time will be increased by factors such as extensive racking, machinery to work around, removal of a coating, heavy grinding, or other construction or building-related obstacles. We will be happy to look at a floor and layout and give an accurate application time estimate.
How Do I Maintain Polished Concrete?
Maintenance for polished concrete is very minimal. However, regular cleaning is still needed. Regular care includes occasional damp mopping to remove dust or grit. You may also consider using some neutral cleaner and conditioner that cleans the surface and leaves behind a dirt-resistant film.
Except for high traffic areas, polished concrete will keep its shine for years. If it should ever dull, it is easy to restore. Sometimes simply buffing the floor with a commercial polishing compound will do the trick. If more touch-up is necessary, the floors can be lightly re-polished with a fine-grit abrasive.
AI Coating also offers Polished Concrete Maintenance Programs tailored to meet each customer's long-term concrete polishing maintenance needs. Our polished concrete maintenance programs range from Full-Service Solutions to Self-Service with Support Programs.
What are the Conditions to Avoid to Maintain Polished Concrete?
- Standing liquids of any kind, including water
- Detergents containing hydroxides or sulfates
- Acidic or caustic cleaners; acidic detergents will etch the surface over time and dull the floor's finish
- All contact with any acids
- Treated dust mops or sweeping compounds
- Bleach or any acidic/harsh chemicals
- Aggressive scrubbing brushes; Strata Grit, Nylo-Grit and other aggressive scrubbing brushes will alter the polished pattern and leave a dull appearance
Is Polished Concrete Environmentally Friendly?
Yes. No solvents or volatile organic compounds are used in the concrete polishing process. It is an odorless, non-flammable, and non-hazardous system.
Is Concrete Polishing System a Coating?
No. concrete polishing is a chemical and mechanical reaction with the concrete itself. When the application is finished, the concrete is still bare, but it has gone through a chemical and mechanical process to protect, harden, and polish the surface. The beauty of the system is that the concrete is protected and polished, yet there is no coating to peel, scratch, or wear.
Are There Any Floors where Concrete Polishing is Not Recommended?
Generally, polished concrete flooring is not recommended where strong acids will come in contact with the floor. However, these are generally very small portions of a facility and the remainder of the floor could still be polished.
Have More Questions about Concrete Polishing?
Contact us and ask any questions about our concrete polishing services. We'd like to help!